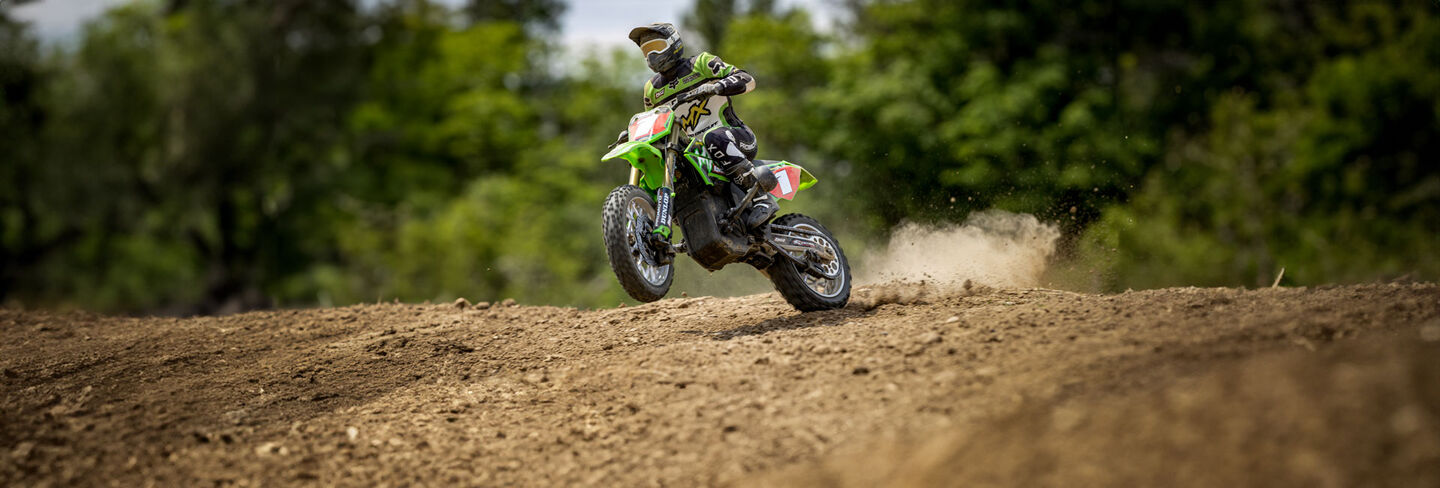
Promoto-MX RC Motorcycle
Customers agree, the Promoto-MX has raised the bar in RC Motorcycle performance. Mechanical and electronic technologies work in harmony to accurately reproduce the full moto experience.